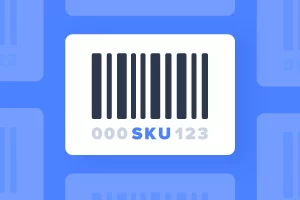
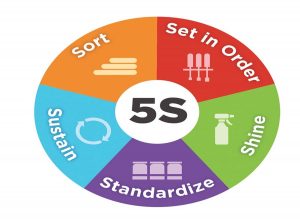
Stay tuned for updates
Stock Keeping Unit & 5S
Whenever a person starts a new business or opens a new shop, they have to face a lot of challenges. Keeping track of the stocks is one of the issues faced by many shop owners and businesses. Stock keeping unit(SKU) helps keep track of inventory in stores.
A stock keeping unit is a unique bar code consisting of alphabets and numbers which can be scanned to get product details like manufacturer, size, type etc. It is usually of 8-12 characters. Two different products cannot have the same SKU. For example,
RB-BLK-7
The above code is for a Reebok shoe of black colour in size 7. There can be numerous codes that can be created for various products based on business requirements. However, it is advisable to not start an SKU with the number 0.
SKU vs UPC
⦁ Stock keeping unit are alphanumeric codes while Universal product code consists of only numbers.
⦁ SKU can be of any length whereas UPC is always of 12 digits.
⦁ SKU is unique for each retailer while UPC is the same for every retailer.
Benefits of Stock Keeping Unit(SKU)
⦁ Stock keeping units help manage stock efficiently.
⦁ SKU help identify how many units of a product are sold. This in turn help finds sales figure and determine profit.
SKU Rationalization
It is a process that involves taking decisions whether a particular product should be kept or removed from the inventory. SKU rationalisation is done based on relevant sales data.
The product which is not getting sold for a longer period faces wear and tear and becomes spoiled. SKU rationalisation help identifies these products. The company can focus on products that are sold faster and make more profits.
5S :
Every organisation be it a large one or small desires to be successful. Achieving success depends on various factors like increasing efficiency, reducing waste. Organisations always wish to accomplish more work in less time at a low cost. This is when 5 S principles are used by organisations to fulfil their goals. Toyota company is credited with the development of the 5S methodology. The company encouraged its employees to focus on every aspect of production from start to finish. This led to minimizing waste and an increased outcome with complete employees satisfaction. The term 5S consists of five Japanese words seiri, seiton, seiso, seiketsu, Shinsuke. The English translation of these words is sort, set in order, shine, standardize and sustain.
5S is a method by which the workplace gets organized and helps reduce waste. The implementation of 5S leads to a safe, clean and efficient workplace.
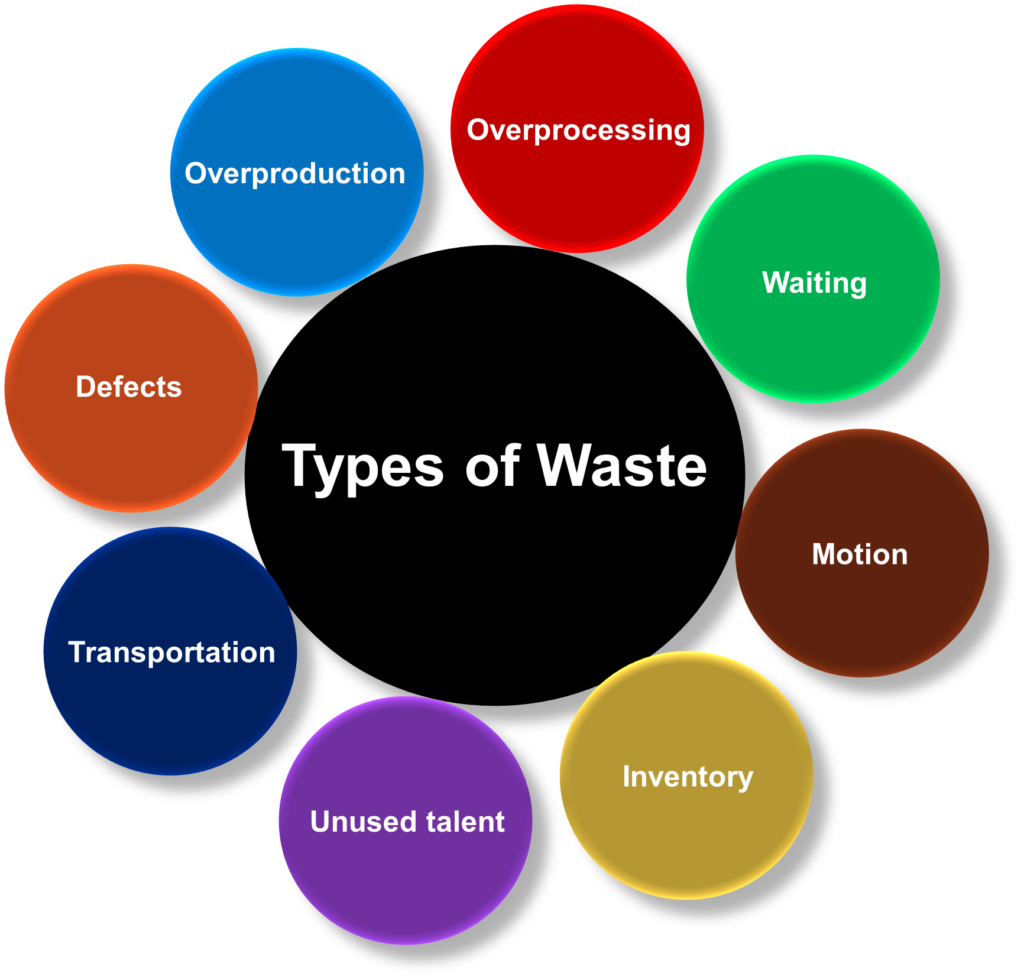
Different Types of Waste
It is essential to understand various types of waste in an organisation which will help in the proper application of 5S principles. The various types are as follows:
Overproduction: When excess products are made then required leads to overproduction. It should be avoided and proper restriction should be applied to the number of goods produced.
Transport: Excess transportation of goods results in damage and fatigue to employees. There should be proper planning and management to avoid unnecessary transportation.
Inventory: There is no point in keeping unnecessary stocks and getting space occupied. This is usually the result of over-purchasing or overproduction and it should be avoided.
Motion: Undesired movement or motion of people which does not help in any production process leads to motion waste. All necessary tools and equipment should be placed in one area from where it can be easily accessible by everyone.
Defects: Production of goods that are not compatible have to be repaired. Many times some products cannot be repaired and have to be put in scrap. Rebuilding takes more time, manpower which leads to less productivity.
Waiting: At any point in time when people have to wait for tools, information or any other thing. This leads to a loss of time and resources.
Over-processing: Performing unwanted steps and using wrong tools and equipment leads to over-processing. There should be proper training given to employees so that they follow the right guidelines.
Unutilized Talent: This refers to the engagement of employees in activities where their potential is not fully utilised. There should be an environment where employees’ ideas are heard and implemented. There should be proper communication among management to avoid waste of talent.
To eliminate the above-discussed waste we have to implement the 5S methodology.
Sort
Sorting is the first step in 5S which involves reviewing all the tools, equipment needed in the workspace. This will help recognize items that are important to get the work done. While those items which are not essential should be kept aside. Inventory waste could be eliminated by sorting.
Set in Order
After identifying essential items, it is important to organise them and make sure they are kept in a specific location where it is easily accessible by everyone. Motion waste can be removed by setting in order.
Shine
Once everything is organised, it is important to clean the workspace. This involves removing dust and trash from tools, machines, and surfaces. A dirty workplace leads to many problems like machinery failure and safety issues for workers.
Standardize
This is the most important step of the 5S methodology. It involves creating standards by which the first three steps of 5S are assessed and sustained. The standards include checklists, work instructions and other documents.
Sustain
This step involves creating an audit system. Sustain convey the need for the 5S system. To sustain the 5S system employees should be rewarded and recognized for their work which leads to employees satisfaction.
5S + 1
Apart from the usual five steps, some organisations have added another step and renamed their process as 5S + 1. The additional step is safety. This step is added to create an environment where workers feel safe.
Conclusion
In today’s competitive world it has become essential for organisations to make use of technology. Any organisation be it small or large can benefit from both stock-keeping units and 5S. SKU and 5S help in getting organised and becoming efficient. This leads to more profit and helps organisations grow.